- Armor Blog
- Consumer Education
- How are Exhaust Valves Cooled in Internal Combustion Engines?
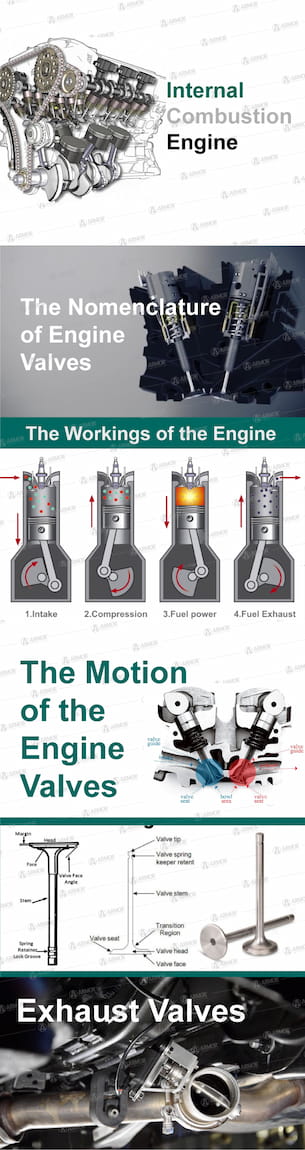
Exhaust Valve of Internal Combustion Engine
Controlling the circulation of gas or liquid into or out of the pistons of an internal ignition engine is accomplished through use of valves. When building an engine, the intake and exhaust valves must be placed precisely. The rocker arms work in tandem with them to guarantee that the doors open and close in the correct sequence. Due to their dual role of blocking or allowing flow, they are very similar to a wide variety of other valves.
Engine valves come in a wide variety of shapes, sizes, and materials, and this article will cover all of them. Valve operation in a typical internal combustion engine will be briefly discussed…
The Nomenclature of Engine Exhaust Valves
The great majority of engine valves are poppet valves, which are characterized by the popping action that occurs when the poppet is moved up and down. These exhaust valves have a conical-shaped valve head that fits against a machined valve seat. This configuration prevents any liquids or gases from going through the valve. Due to the fact that they resemble mushrooms, they are frequently referred to by the nickname “mushroom valves”
The Workings of the Engine
The two most common types of intake and exhaust valves found in internal combustion engines thatuse a four-stroke or four-cycle oil are known as intake and exhaust valves respectively. In order to allow for the entrance of an air-and-fuel mixture into the engine’s cylinders, the intake valves of the engine is opened before the compression and ignition processes take place. After the ignition process has started, the exhaust valves are opened so that the exhaust gas may be discharged in a more effective manner. This makes it possible for the engine to produce greater power.
The motion of the Engine Exhaust Valves
The linear movement of the engine valves is driven by the camshaft. Numerous cams on the camshaft is responsible for converting the rotational motion of the camshaft into the linear motion of a valve. The number of valves and the number of cam lobes in an engine are inversely related.
Cylinder valves in modern, high-tech engines with internal ignition can be found in a wide variety of shapes and sizes. This is because the shape and size of each valve is controlled, in large part, by the design and function of the cylinder. Single-valve intake and exhaust systems are common in lawn mowers and other outdoor motor equipment. There can be as many as five valves per cylinder in larger engines, such as those with six or eight pistons, although there can be as many as four in smaller engines.
Components of the Engine Exhaust Valves
Internal combustion engine valves are subjected to significant amounts of stress as a result of their role in the engine’s operation. Typical intake valve materials include chrome, nickel, and tungsten steel. These are only a few of the many options available to manufacturers. This is due to the fact that these valves are able to operate at lower temperatures than other valves. Exhaust valves that are designed to endure temperatures that are higher than 2,000 degrees Fahrenheit may be constructed out of materials such as iron and nickel, silicone chromite, or mixtures of copper and chromium.
To further enhance their mechanical qualities and wear characteristics, engine valves might be coated or finished with coatings and surface treatments. There are a variety of finishing procedures that fall under this category, such as chromium plating, phosphating, nitriding, and swirl plating.
Restricting the heat flow into the valve can be achieved by:
- Minimizing the heat inflow areas, i.e., valve head and neck, either by modifying the shape of the valve or by extending the valve guide as close as possible to the valve head.
- Usage of thermal barrier coatings on the heat inflow areas.
Heat outflow can be enhanced by :
- Modifying the design of the seat insert and valve guide to maximize the heat outflow areas
- Minimizing the length of the thermal paths between the valve and cooling jacket in the cylinder head.
- Replacing the valve, seat and guide materials with others of better thermal conductivity.
Conclusion
Controlling the temperature of the exhaust valves is paramount for proper functioning of engines and for the long lifespan of valve train components.