- Armor Blog
- Industry
- Industrial Lubrication Tagging and Labelling Importance
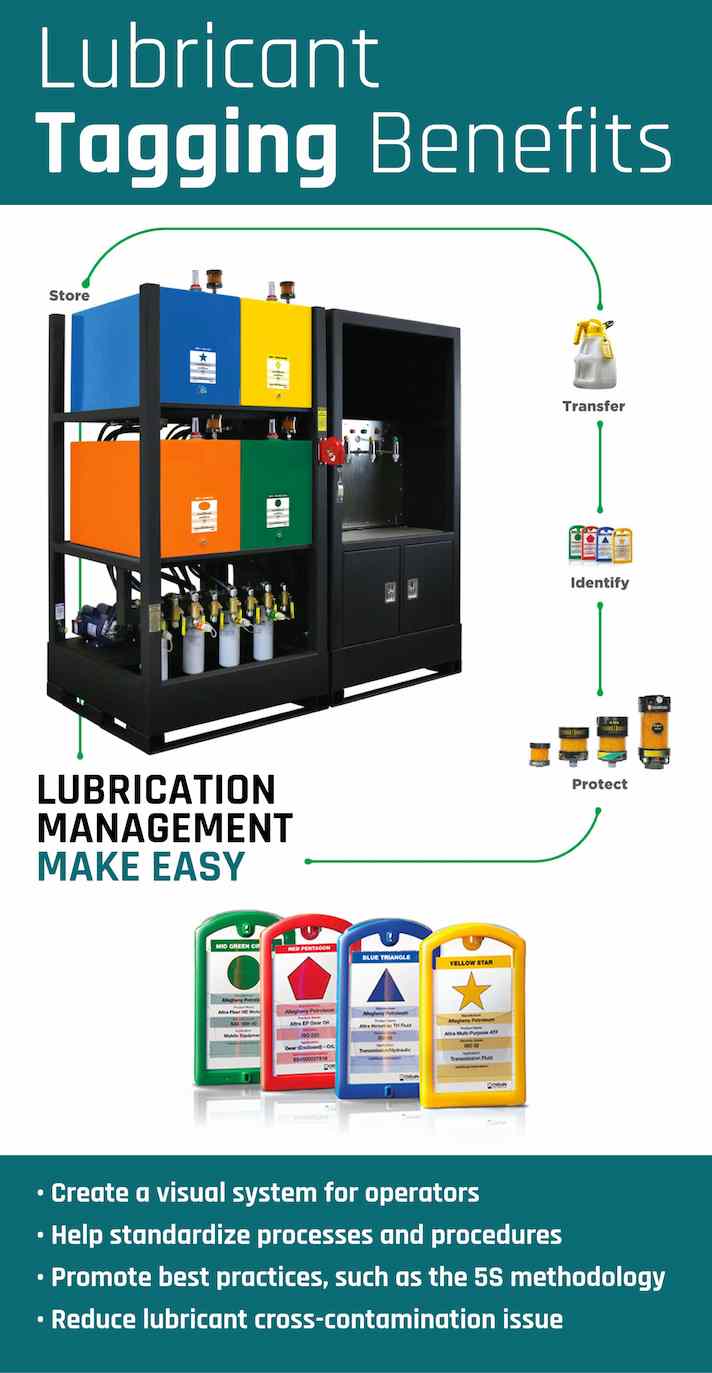
Why Every Industrial Facility Needs Lubrication Tagging?
Major maintenance and construction industries are often cluttered with machines, conveyors, and other large industrial equipment. In order to keep these machines running smoothly and efficiently, their operators need to know how to properly lubricate them. Unfortunately, many of these factories don’t have the funding or manpower to install specialized lubrication tagging, tracking, and labeling equipment. That’s where lubrication tagging and labeling come into play.
By attaching tags or labels to all of the greases used in these industrial facilities, operators can quickly look up the information they need when servicing the machinery. This information can include the type of grease used, its viscosity range, as well as other important specs. By doing this in a centralized location, it becomes much easier for workers to ensure that they’re using the appropriate lubricants for each machine.
The Lubrication Identification tag identifies which machine requires which lubricant based on a coding system. Codes can be colors, shapes, or anything else that lets you know which lubricant to use. Lubrication Identification systems are underutilized in many facilities.
Lubricant cross-contamination is one of the root causes affecting asset reliability. The proper identification of lubricants creates a visual, color-coded “chain of custody,” from the storage room to the equipment, and reduces human error.
Lubrication Tags and Labeling Benefits
- Lube tags help ensure the proper lube is being used and improve machine reliability.
- lubricant Identification System (LIS) provides a generic system that doesn’t rely on product names.
- Steel lube tags should be used as they are hard to fit.
- Lubrication tags tell you the type, weight, size, composition, and condition of the lubricant.
- This information can be used as evidence in environmental or safety cases.
- It can help you to make informed decisions regarding when and how to replace components.
Implementation of Lubrication Tagging and Labeling:
The following steps are required in setting up and maintaining a simple lubricant-ID control system:
- Work with your lubricant supplier to determine the minimum number of lubricants required for use on-site.
- Catalog and document all lubricant points and reservoirs by machine.
- Print out individual lubricant ID nameplates, stickers, or tags.
- Remove all old lube references from the machine.
- Symbolize and color each recommended lubricant on the consolidation list,
- Institute a change-notice requirement process to remove, replace, or add a lubricant in the plant, or to the ID control list.
- Engineering, purchasers, issuers, storage, and application personnel should be trained on the new lubrication identification system.
Lubrication Tagging and Labeling in Industrial Facilities
Mixing incompatible lubricants can cause seal expansion, shrinkage, additive precipitation, loss of anti-wear performance, and demulsification issues.
The hypothetical plant has six types of oil, and any one of them can be used wrongly. By labeling the oil drum, bulk tank, S&R container, and finally the machine that uses the oil, lubrication becomes foolproof.
When lube tags are properly installed and maintained, they provide a history of the lubricant oil or other fluid in the system. This information is invaluable for maintenance planning, troubleshooting operations tasks, asset management decisions (e.g., disposal), environmental analysis (e.g., emissions), litigation support (e.g., product liability), and other reasons related to safeguarding public health and safety or protecting valuable equipment or resources.
Some essential aspects of tag installation include accurate installation; correct positioning on the component; proper spacing on each tag; good adhesion between adjacent tags; proper repeatability when punching out tags from sheet material; legibility of the tag data under various conditions including weathering, earthen deposits buildup or graffiti; the permanence of tag data over time in most environments unless intentionally defaced/destroyed by operators and long-term retrievability if necessary for investigative purposes.
In Conclusion
The need for proper lubrication tagging and labeling becomes increasingly important as industrial facilities become increasingly automated. With the use of tagging and labeling along with lubricants testing, manufacturers can ensure that their machines are running smoothly and free of contaminants. Not only does this benefit the facility, but also the employees who use these machines daily.
Few organizations use lubricant tags to their full potential, while some fail to use them at all. Lube tags help ensure the proper lube is being used and improve machine reliability. There are many solutions on the market for color-coding devices that are commonly used in a lubrication program.
Proper labeling and tagging of industrial lubricants is crucial for ensuring optimal equipment performance and minimizing downtime. By implementing a robust labeling system, you can streamline maintenance processes, reduce errors, and extend the life of your machinery.
Want to learn more about lubricant storage and handling best practices? Check out our blog post on best storage practices for additional tips and insights.