Lubricant Storage and Handling : Best Practices
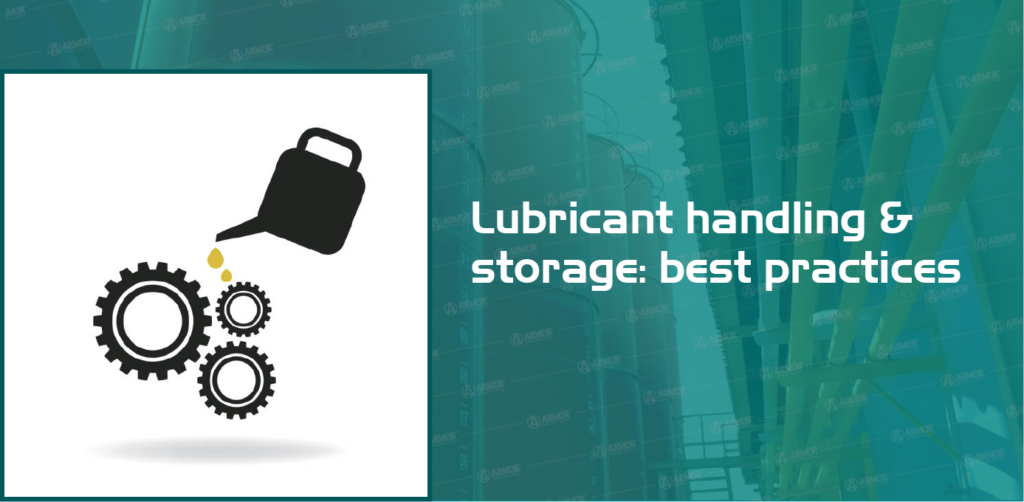
When dealing with lubricant storage and handling, there are a few conditions that need to be taken into account, to preserve your products safely for longer, and without deterioration or contamination all to ensure the best quality and longevity of your products.
As with all commercially available lubricants and all sealed material, there needs to be care put into how the lubricants are labelled, handled, stored, and subsequently used to ensure that deterioration does not take place – mismanagement can lead to ruined and/or expired products, and the loss off efficacy in motors that use these lubricants.
Shelf-life & Proper Labelling
In perfect conditions, the shelf-life of lubricants can vary between six months up to three years, depending on their additives. This, of course, is the case when environmental conditions are met perfectly during storage and proper usage is ensured to avoid contamination and degradation.
When receiving lubricants from the manufacturer, confirm the shelf-life of the product and it’s recommended use-by dates. During storage, ensure proper care and handling of the container so that labels do not get ruined or removed, as this can easily happen during mishandling of the packaging regardless of its container and packaging. In addition, implementing a labelling and inventory system of your own is also advised.
Lubricants can quickly cause harm to the motors if used beyond their shelf-life, therefore a “first-in-first-out” (FIFO) method is recommended to make sure that older or open lubricant containers get used up first.
NLGI advices the following measures for storing grease in a safe and effective manner:
- First, use the oldest container.
- Containers should be tightly closed.
- Store in a cool, dry indoor place with minimal airborne debris.
- Be sure to clean the outside of the container before opening it to prevent dirt from getting inside of it.
- It’s recommended to get grease to a suitable dispensing temperature shortly prior to use.
- Tools for handling grease should be clean.
- Grease should be used to fill any gaps left in containers after they have been partially emptied and before they are leveled or sanded.
- Grease cartridges (tubes) should be stored vertically, with the cap removed..
Sometimes, the lubricant labelling process gets missed. If lubricants aren’t properly labeled, cross contamination is quite likely to occur. As a result of mixing two lubricants, lubricant cross contamination might have disastrous consequences. Instead of bulk storage equipment, this occurs more commonly with dispensing systems than with bulk oil storage systems.
Handling
When receiving containers from lubricants manufacturer, careful handling needs to be implemented, this includes but is not exclusive to using proper equipment to carry containers, whether drums, barrels or bottles packaged in bulk, to ensure that they do not fall and damage seals or packaging, a forklift is an advised equipment to use. Throwing, dropping or rolling containers can damage them and will immediately result in the product becoming contaminated due to leakage or breaking of seals. Even though larger containers such as barrels and drums are meant for several uses, mishandling them can also lead to damage.
Storage Sites
Storage can be done either indoors or outdoors, but a dedicated indoor storage facility for lubricant storage and handling is recommended as it is the safest way to ensure that environmental conditions do not deteriorate lubricants or cause environmental contamination. A dedicated storage facility would also ensure that packages in bulk are stored securely without the risk of falling or sliding over, and it also ensures that drums and barrels are stored on an appropriate surface that doesn’t damage the packaging of the containers themselves.
The storage site bust be designed to be operative and expandable to meet all the necessary requirements.
Some best practice tips for storage sites are as follows:
- Making sure the storage area has as little airborne particles as possible.
- Covering containers with plastic sheets to ensure that moisture does not get in, nor does water or airborne particles.
- Temperature is maintained throughout the storage area as per manufacturer’s direction.
- Smooth and level flooring to avoid tipping or damage to the containers.
- Enough space to fulfil the FIFO method while rotating through the inventory.
Environmental Conditions & Contamination
Lubricants can undergo contamination and deterioration if exposed to the elements or foreign materials, which is why a dedicated indoor storage facility is recommended while considering for lubricant storage and handling. However, even an indoor area can present danger to lubricants.
Different types of environmental contaminations and their fixes are as follows:
- Temperature: Varying or extreme temperatures can cause chemical changes in lubricants, depending on their additives. They can also result in the deterioration of the packaging itself, giving way for other forms of contamination. Therefore, a temperature-controlled storage facility is of utmost importance, so is the usage of fireproofing.
- Light: Direct sunlight can also lead to temperature changes and a degradation of the container itself.
- Water & humidity: Due to the chemical nature of lubricants, they have a tendency to absorb moisture, this can lead to a drop in the efficacy of the lubricant itself once used. Storage facilities must be cool and dry, making sure that the area is properly sealed as well.
- Airborne contamination: This is especially necessary in industrial settings where other things are being manufactured or used, foreign materials that mix with the lubricants can cause contamination. A properly sealed facility is important, so is ensuring that each container is tightly sealed as well.
Quality Control
It’s necessary to verify the quality of lubricants given by the lubricants supplier to confirm that the correct product is being produced and that it meets with the specified up to date requirements.
Performing oil analysis is a valuable technique for ensuring that your lubricants satisfy their specifications and will indicate the following:
- Base-stock quality
- Performance levels of lubricants
- Performance characteristics of thickeners/grease
- Quality of additives and concentration
Waste & disposal
Ensuring proper disposal of lubricants and empty containers is just as imperative since lubricants can present a fire hazard.
Waste lubricant should be disposed in secure containers with properly sealable lids as spills can cause a health and environmental hazards. All empties containers and packages that once contained lubricant need to be disposed in appropriate recycling bins or facilities as they are eligible to handle corrosive and flammable material.
It is also dangerous to attempt to cut down drums or barrels that once contained lubricants as it can cause a fire hazard.
In conclusion
Ensure that the lubricants provide the best efficacy in the motors they are used in, it is crucial to protect both the containers and the lubricants themselves from the elements, environmental contaminants, and other airborne particles, it is also recommended to ensure proper usage in a timely fashion to avoid degradation through exceeded shelf-life. All in all, following lubricants manufacturer directions and labelling, while going through proper lubricant storage and handling guidelines can ensure the longevity and effectiveness of your lubricants.